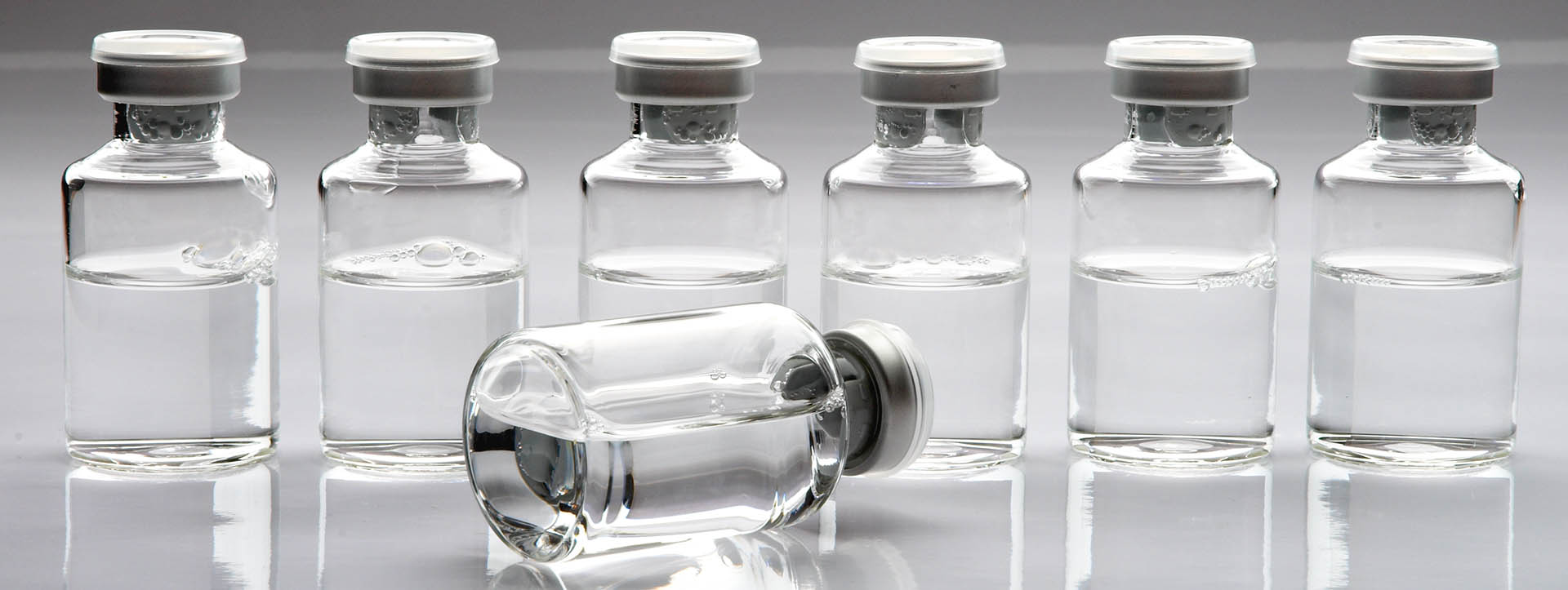
Preparation of reference standard test sets
Potential sources of contamination or defects that may occur during the production of pharmaceuticals are determined individually by each company through an internally conducted risk analysis. The following defects and particles, among others, can arise during the production of parenteral pharmaceuticals:
-
- Container defects
E.g. scratches, cracks, residue, crimping cap and stopper defects
- Container defects
- articles in the solution as well as particles adhering to the container or the container seal
E.g. glass, fibers, rubber, plastics, metals
- Deviating product characteristics
E.g. discoloration, turbidity, incorrect filling volumes
Based on the risk analysis conducted by the customer, M.A.S… creates individually defined reference test sets for each client.
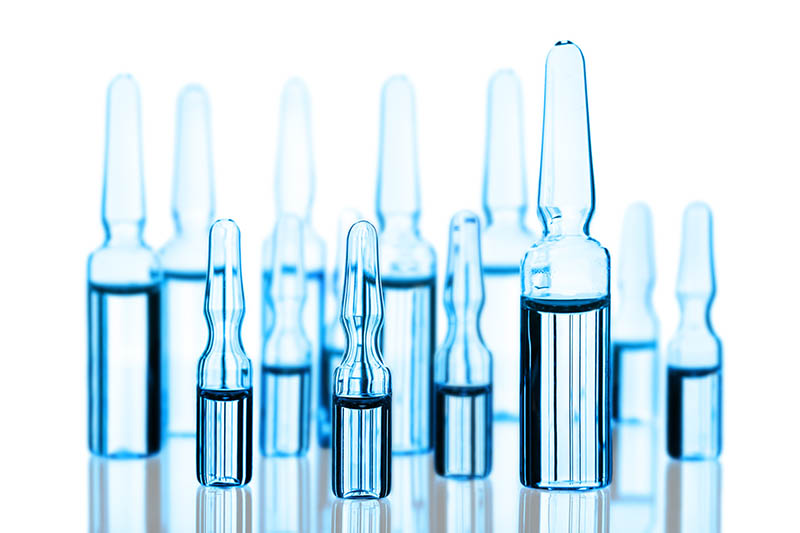
Reference standards for liquid pharmaceuticals
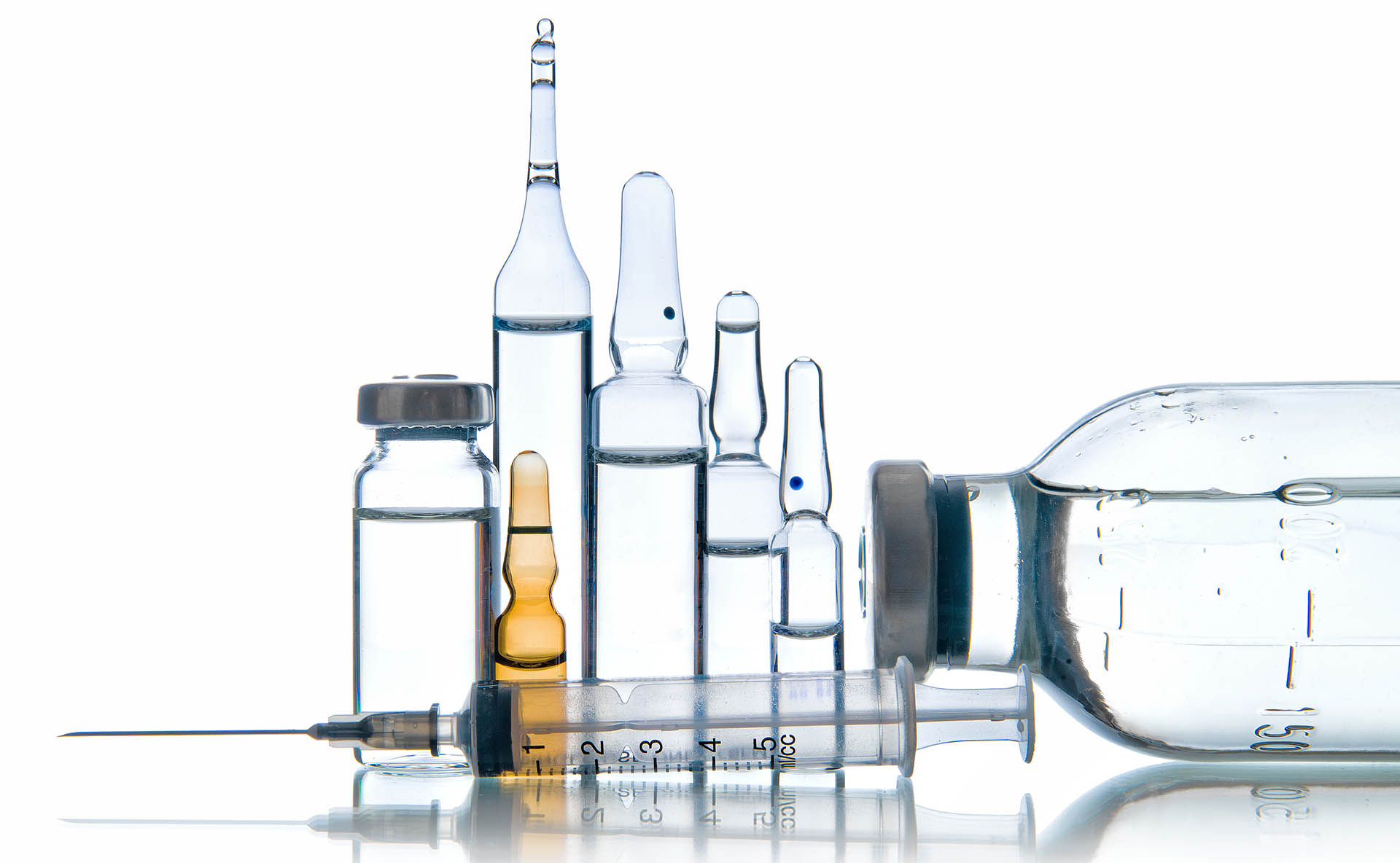
Reference standards for liquid parenteral pharmaceuticals are produced by altering the container directly. For this purpose, pre-filled containers from our customers can be used or filling can be done by M.A.S… Reference standards can be prepared for the following container formats:
-
- Vials
- Prefilled syringes
- Ampoules
- Cylindrical ampoules
- Infusion bags
- BFS containers
Measured particles can also be provided on microscope slides with depressions if the customer wants to prepare the samples on-site. Measured particles, supplied with a detailed documentation.
Creation of reference standards with particles
For the preparation of particle samples, materials provided by the customer or particles from the extensive M.A.S… particle library can be used.
Particles of glass, metal or plastic can be prepared starting from a size of 50µm. Due to the thickness of fibers and hair we recommend their preparation from a fiber length of 100µm.
Each particle sample is provided with detailed documentation. All data are digitally calculated and stored using a stereomicroscope and the modified image program analySIS. The documentation consists of a certificate, detailed particle data (including size, circumference, form factor, diameter) and a microscopy image of each prepared particle.
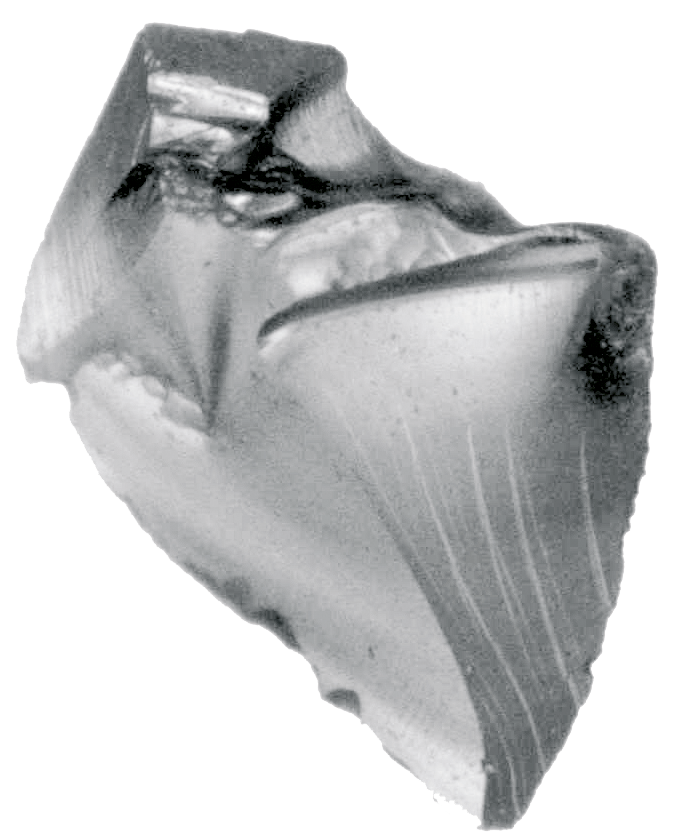
Creation of reference standards with defects
Containers that are rejected during visual inspection due to defects may have the following deficiencies, among others:
-
- Container defects:
Scratches, cracks, contamination, chipping
- Seal defects:
Incorrect seal damaged stopper, incomplete crimping - Product characteristics:
Discoloration, turbidity, incorrect filling volume
- Container defects:
The various defects are simulated in the M.A.S… laboratory and documented in detail. Container defects such as cracks or chips are prepared according to customer specifications (e. g. in different size ranges, at different positions of the container) and then digitally measured. Deviating product characteristics such as turbidity or discoloration are manufactured according to customer’s specifications.

Preparation of lyophilized reference standards
Freeze-dried pharmaceuticals are often not suitable for the preparation of reference standards due to the low stability of the lyo cake.
For the preparation of lyophilized reference standards, M.A.S… has therefore developed a lyo stabilizer formulation. Because of the high stability of the lyo cake, it is well suited for the quality control of freeze-dried products. At the customer’s request, the lyo cake can be adjusted in color if necessary. The stabilizer mixture is filled into the containers provided by the customer and the requested defects and particles are prepared. The samples are then lyophilized in our Christ freeze dryers.
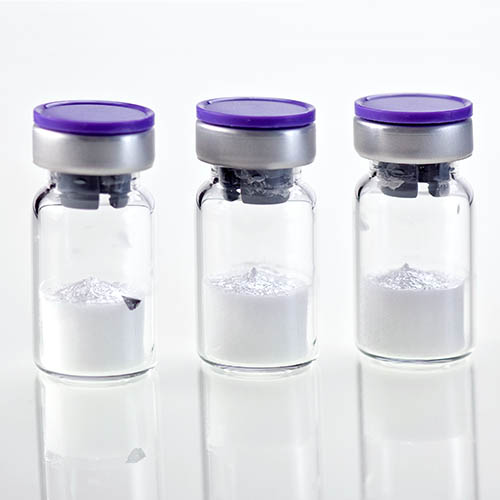
Preparation of reference standards with pinholes
Container Closure Integrity Testing (CCIT) is an important aspect of quality control in the pharmaceutical industry. For this purpose, M.A.S… offers the creation of laser-drilled holes (pinholes) in containers. Pinholes can be created from a size of 5-10µm in ampoules, pre-filled syringes, cartridges, and tubular glass vials. The pinholes can be used for various test methods such as immersion tests with a dye or high voltage leakage test.
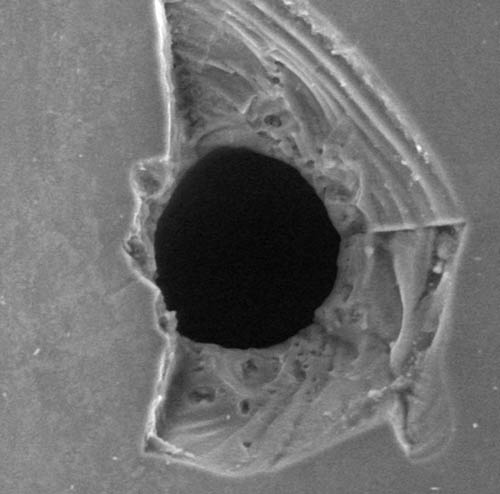
Media fill
A critical process in the production of parenteral pharmaceuticals is their sterile or aseptic filling. To validate the production line, so-called media fills must be conducted. For this purpose, a nutrient solution is filled in place of the product and, after a defined incubation period, subjected to a thorough microbiological and visual inspection.
For training purposes, M.A.S… creates the desired turbidity patterns based on the nutrient solution. Microbiological contamination can be simulated using a standard solution. The degree of turbidity of the media fill samples is adjusted according to customer requirements.
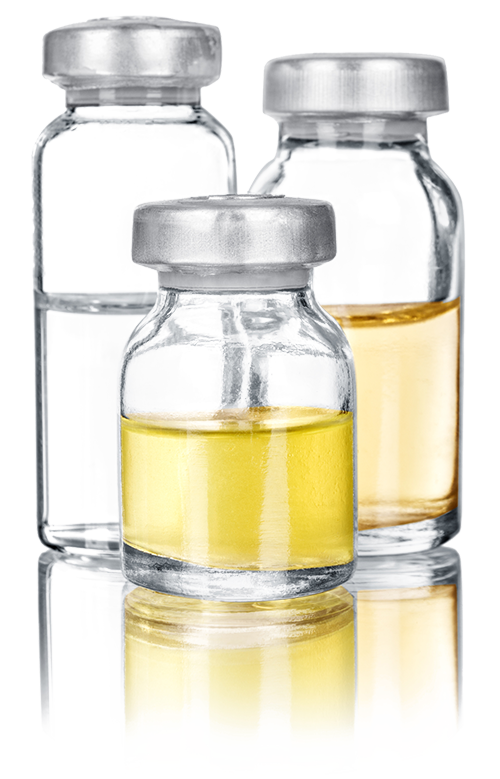